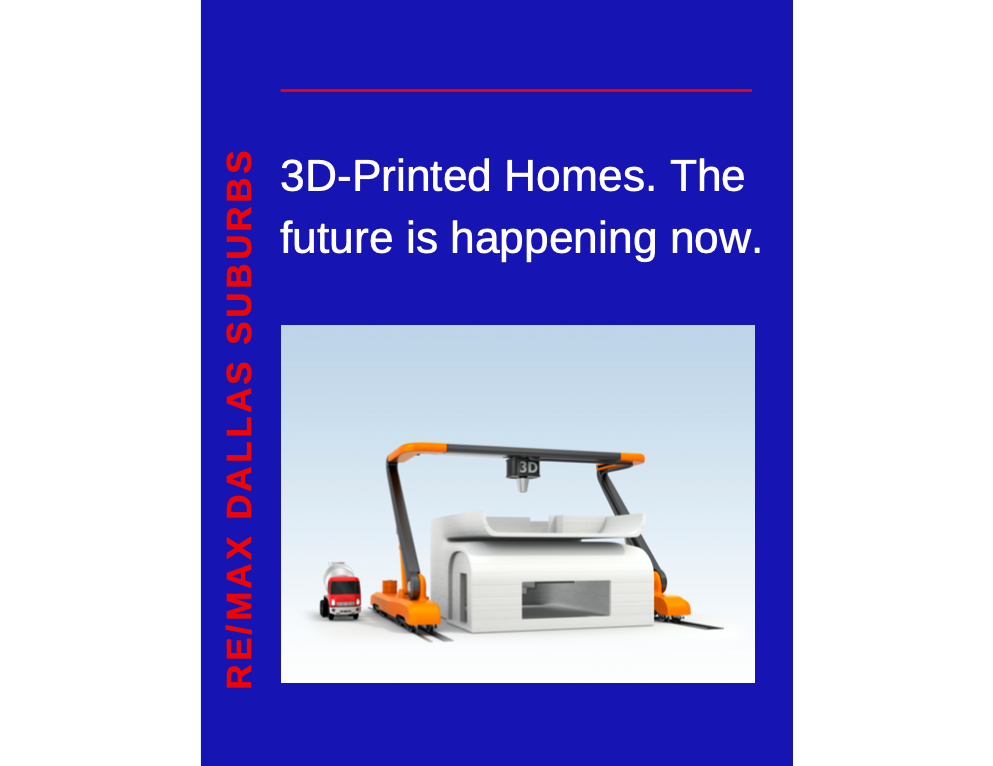
BEHIND THE SCENE
Not too long ago, printing a home was more or less a futuristic dream. But now it is a reality that is taking shape fast, thanks to a new wave of 3D-printing technology companies coming forth with solid solutions. Just think. Less time. Less costs. More happy homeowners than ever before. Truly 3D-printing is poised to revolutionize the home construction industry.
Just imagine, fast-built, sustainable, affordable housing!
With home prices rising and housing inventory becoming tighter every day, it is no small wonder that buyers and builders alike are turning to alternative options like 3D-printing technology. In fact, some in the housing industry say this futuristic approach could transform home construction on a broad worldwide scale.
To give you an idea of how 3D-printed homes are made let’s take a look at Mighty Buildings—a construction technology company based in Oakland, California. Their 3 D-printed homes are printed with a synthetic stone material they invented and named Light Stone Material. The 3D-printed panels are applied to a steel frame at their factory. Robots add insulation and interior woodwork. Brick or siding faux finishes can be added to the exterior. Cabinets, HVAC systems, and appliances are added by human workers.
Another company leading the way is Austin-based construction technology company ICON. Their process incorporates their large-scale construction printer named the Vulcan that relies on robotics. Built for precision and speed, the Vulcan is capable of printing resident homes and structures up to 3,000 square feet. To create their structures, beads of ICONs pliable, proprietary cement-based material called Lavacrete oozes from the printer in ripples that stack and harden into a wall with curved corners.
Which brings up another point worth mentioning. Because 3D- printing uses slopes and curves, many believe it will allow more design freedom in the construction industry in the future.
It’s hard to believe, but it’s true—350-square-foot tiny homes that can be created in under 24 hours to 1,900 square-foot homes that can be printed in less than 48 hours using a minimal number of workers. All at 30% to 40% cost savings. The future of housing will never be the same.
Hi, I’m Suzanne Athey, owner and founder of Team Athey & Remarkable Property Management. I hope you found our blog on 3D-printed homes informative. If you’d like to know more, call me at 469-916-1222, or email me at suzanne@teamathey.com. I’d love to visit with you and answer all your real estate questions.